Chris Robben
SIX-S GmbH, Hinter der Kirche 1A, 22880 Wedel, Germany
This example originates from the mining industry with some parallels to the previous exploration example.
Decision and routing of material into ore and waste streams is achieved using dedicated Particle Ore Sorting (POS). POS is a mineral processing method, where particles in a stream are identified individually by a sensor-based detection technology (e.g., X-ray transmission or near infrared spectrometry) and—based on binary classification into ore and waste—are separated using targeted pulses of compressed air (Figure 1).
Figure 1. Simplified flow-sheet of a POS station. The undersize flows from the screens are too small for sorting and are bypassed and combined with the product fraction from the POS equipment. The cross marks the position of sampling the waste fraction.
POS is often physically located separately from other functional units of the process, such as milling and flotation. A POS process island as shown in Figure 2 usually comprises of crushing, screening, sorting and auxiliary equipment, such as the compressor station delivering the compressed air for the physical separation process.
Figure 2. Sorting island installed at the Mittersill tungsten mine in Austria.1
The efficiency of POS depends on two fundamental factors. One is the detection efficiency, i.e. the reliability with which the equipment correctly classifies ore as ore and waste as waste. The other factor is the efficiency of the pneumatic physical separation process.
The value created by a sensor-based ore sorting process often lies in the rejection of marginal waste. The inherited value would not justify spending the costs of processing and is described by the so-called cut-off grade. The sharper the sorting island can operate to this cut-off grade of the separated waste, the more economic value is created. If the grade is lower, additional mass could have been rejected, saving processing costs and debottlenecking the plant for higher grade feed which results in additional revenue. If the waste grade is too high, value is lost to the waste fraction and the ore reserve is underutilised. In mineral processor terms, high grade ore must be recovered, achieving a high recovery of the pay element(s) in question, though the focus lies on controlling the waste grade. A recommended practice is here to install a suitable sampling system on the waste material stream from the ore sorting station. What makes a POS system special in the context of the TOS is that POS processes particles sized 10 mm and larger, necessitating higher sample masses than with smaller average particle sizes due to the Fundamental Sampling Error. As a consequence, it results in the necessity to apply suitable automated mechanical sampling systems.
So far, so good. But what is the decisive increment extraction rate and what should the sampling rate be to discover fluctuations in waste grade over time with a desired fidelity? What if for half of the day the waste grade is too low and for the other half it is too high? Daily sampling would then mask this fluctuation and indicate that the waste grade is exactly on target.
A benchmark case is POS separation with high ore-to-waste and waste-to-ore misplacement, reducing recovery and increasing mass flow towards the main plant. A sampling station collecting increments for a composite day sample averages out the fluctuations of waste grade, even though a Sampling Error may be minimised according to the TOS.
An optimised case addresses optimisation of the sampling protocol. For example, by increasing the increment extraction and the accompanying assaying frequency to better monitor in-stream fluctuations over time. This is mainly an investment in the sampling, sample preparation and assaying operations. It is expected that this will be mainly a proportional increase in operating expenses. Better visibility into in-stream variation combined with a faster turn-around time of assay results makes it possible to optimise the operational parameters of the POS equipment to better follow the variation (i.e. distributional heterogeneity) over time.
This example illustrates the specific sampling challenges for POS technology due to large particle size but is in principle directly transferable to performance monitoring of all process equipment. Equipment control and optimisation must be data driven and process focused using fit-for-purpose sampling equipment and procedures to unlock value along the mineral process value chain.
NPV over identical mine life | |
Base case | $712 million |
Optimised case | $763million |
The increased NPV over the lifetime of a typical mine is $51 million: more than sufficient to pay for the efforts of designing and implementing the optimised sampling protocol and additional assay costs. This is a quite satisfactory investment on the table of any board of directors!
In mineral processing there is so much more to understand and to monitor better, with which to increase efficiency and thereby to increase both profitability as well as sustainability of the industry.
Reference
- C. Robben and A. Mosser, X-Ray Transmission-Based Ore Sorting at the Mittersill Tungsten Mine. Paper presented at the 27th IMPC Chile (2014).
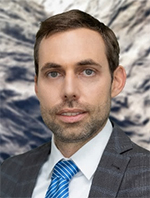
Christopher Robben
Dr Christopher Robben holds a Masters degree in underground mining and a PhD with distinction in mineral processing. He has close to two decades experience in sensor-based ore sorting where he worked in sensor-, process-, and project development globally and is one of the world leading experts in this field. His focus lies on overall business improvement, sound engineering, mineral economics and financial modelling and has got hands-on experience in geometallurgy, process development, project development, pilot operations and production. For the San Rafael Tin Ore Sorting Project he has received the Peruvian Prize for Innovation in Mining that he developed on behalf of the equipment supplier. Christopher Robben is Managing Director of SIX-S, a specialised consulting company with the mission to increase productivity in global mining sustainably, with the application of sensors, sorting, sampling and strategy.
[email protected]